In a major, high-value project – the second at this particular plant in Mexico – NUTEC Bickley will supply a 125m-long tunnel kiln to one of the world’s leading advanced ceramics manufacturers.
Related Services
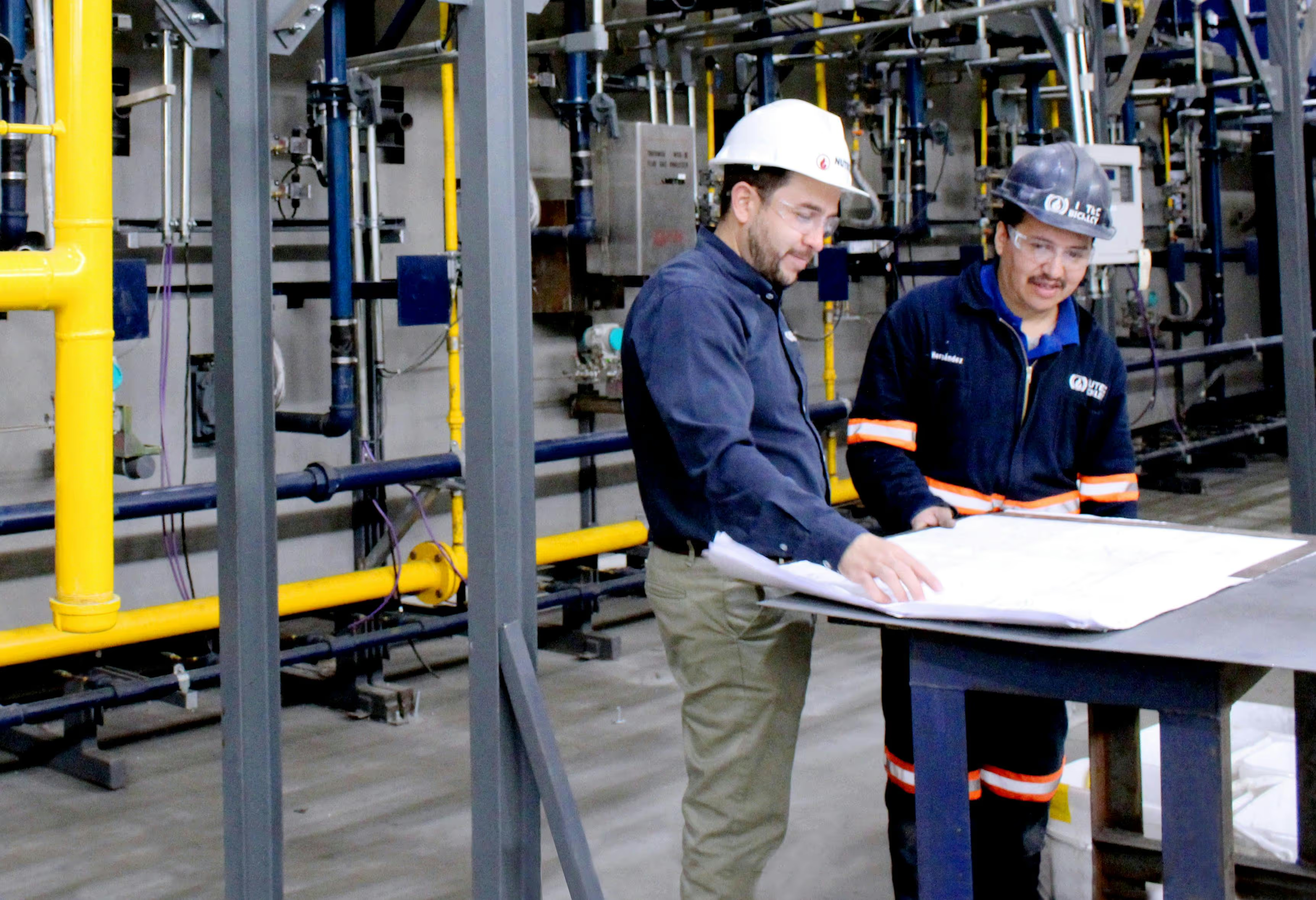
Maintenance Policies
NUTEC Bickley provides Maintenance Policies for industrial furnaces all over the world. Our commitment is to keep your combustion systems in the best possible operating condition with periodic reviews and a process of continuous improvement.
Learn more about our Maintenance Policies
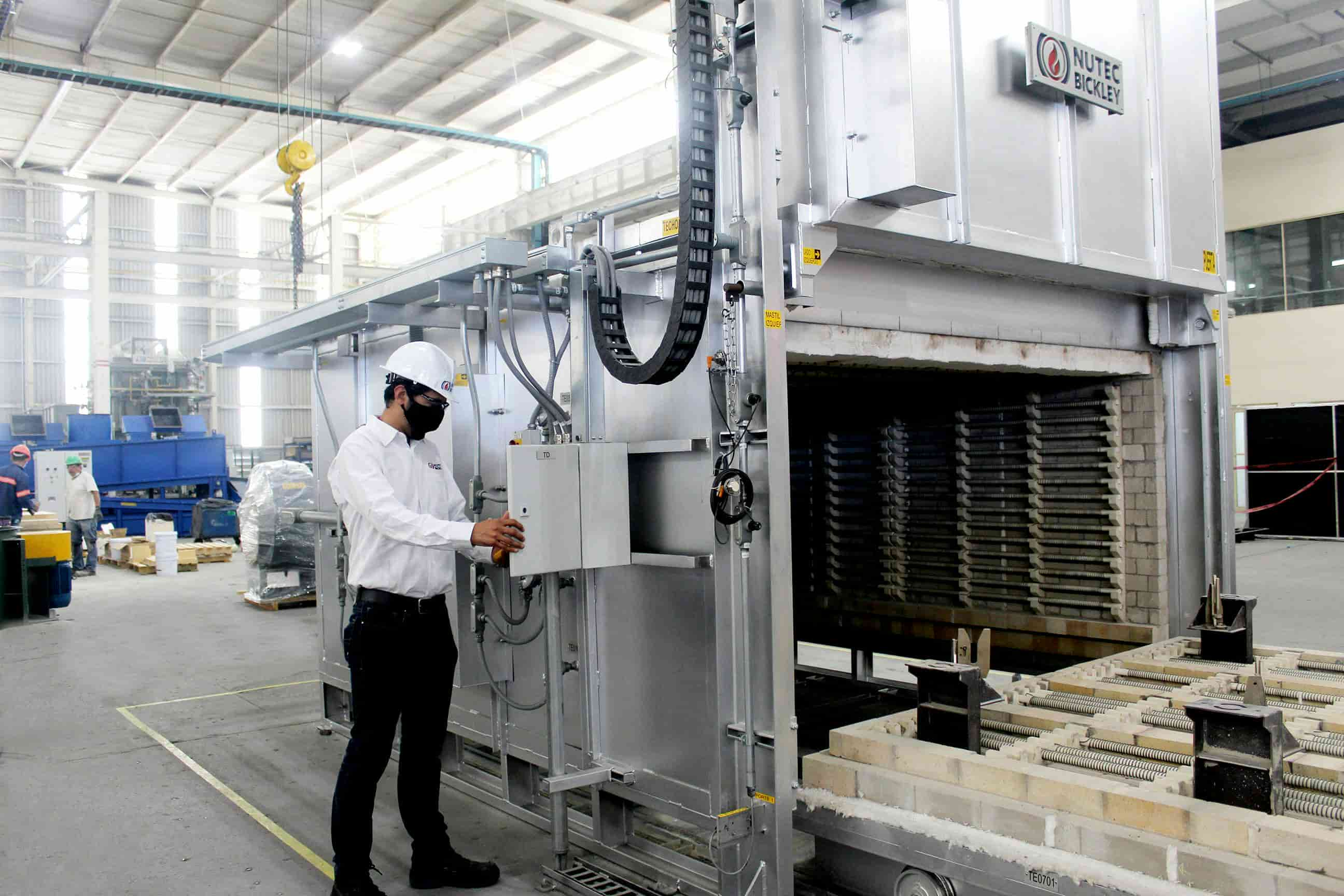
Control Logic Support
We inspect the entire electrical installation, we advise you on PLC, HMI, and SCADA issues and ensure correct programming of your equipment.
Learn more about our Control Logic Support