Industry leading manufacturer, specializing in rotary forging, metal spinning, and the flow forming of aluminum and other alloys into complex shapes.
Tunnel kiln technology
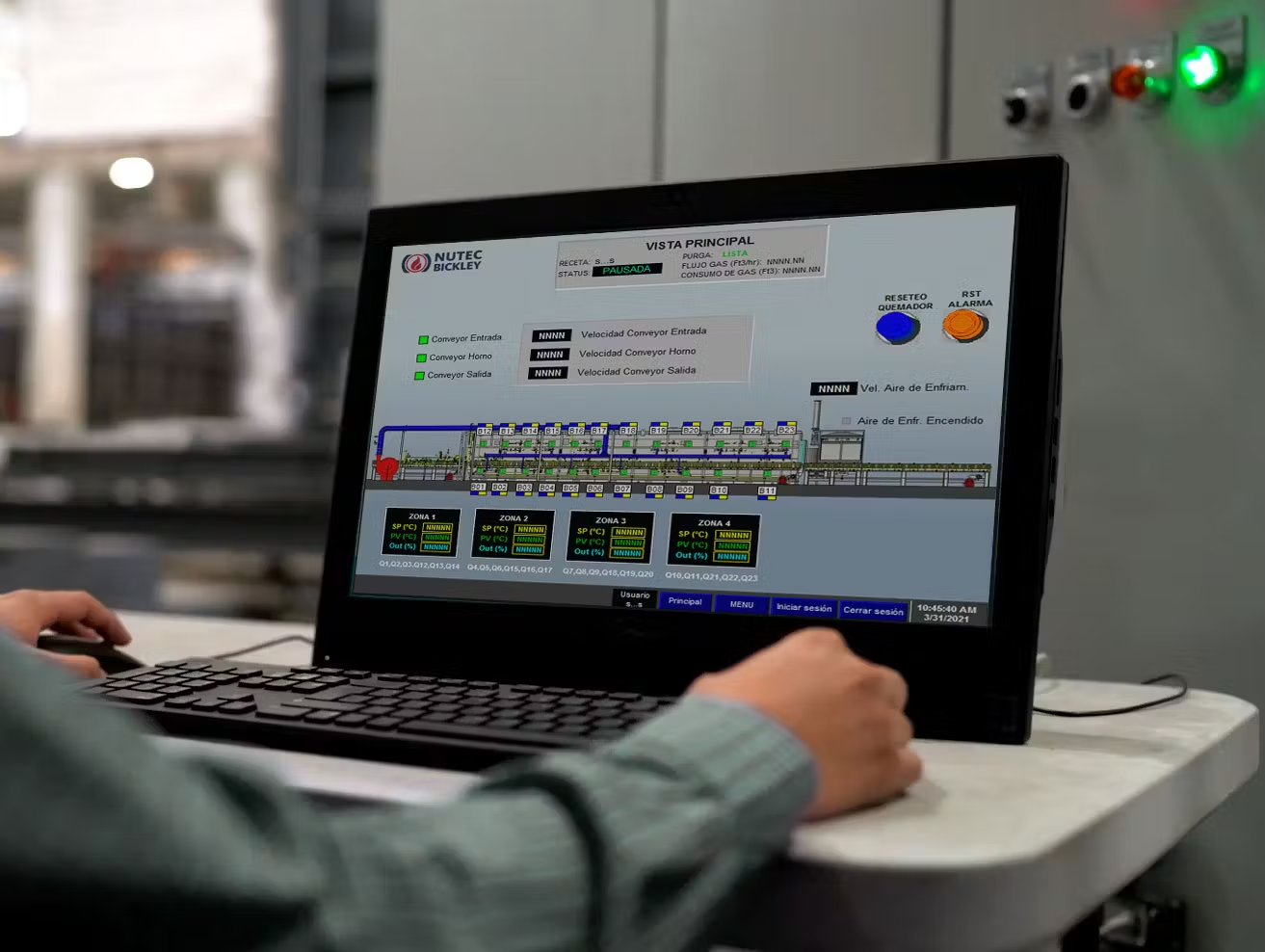
SCADA
With our SCADA systems, kilns operators are able to have complete control of their firing process, enhancing efficiency and productivity.
Learn more about SCADA
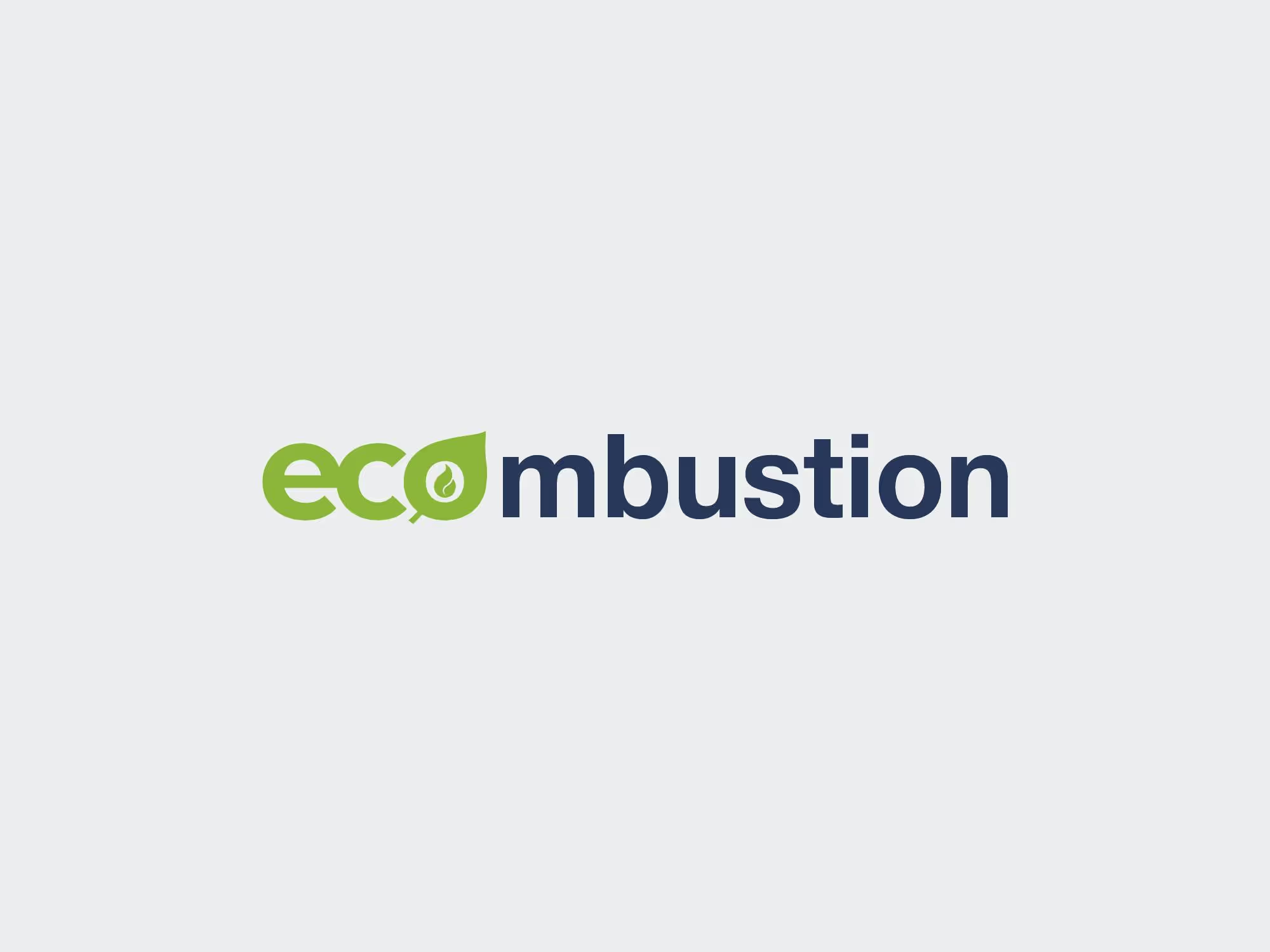
ECOmbustion™
NUTEC Bickley’s proprietary ECOmbustion™ system is an innovative control methodology designed to achieve fuel savings in gas-fired kilns, bringing operating costs down and reducing carbon footprint.
Learn more about ECOmbustion™
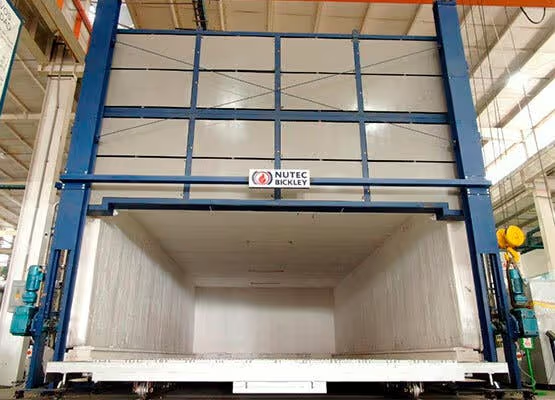
Jointless® Insulation
NUTEC Bickley’s patented ceramic fiber Jointless® modules provides for minimal maintenance, enhanced fuel economy and extended service life.
Learn more about Jointless® Insulation