Industry leading manufacturer, specializing in rotary forging, metal spinning, and the flow forming of aluminum and other alloys into complex shapes.
Technology Offered
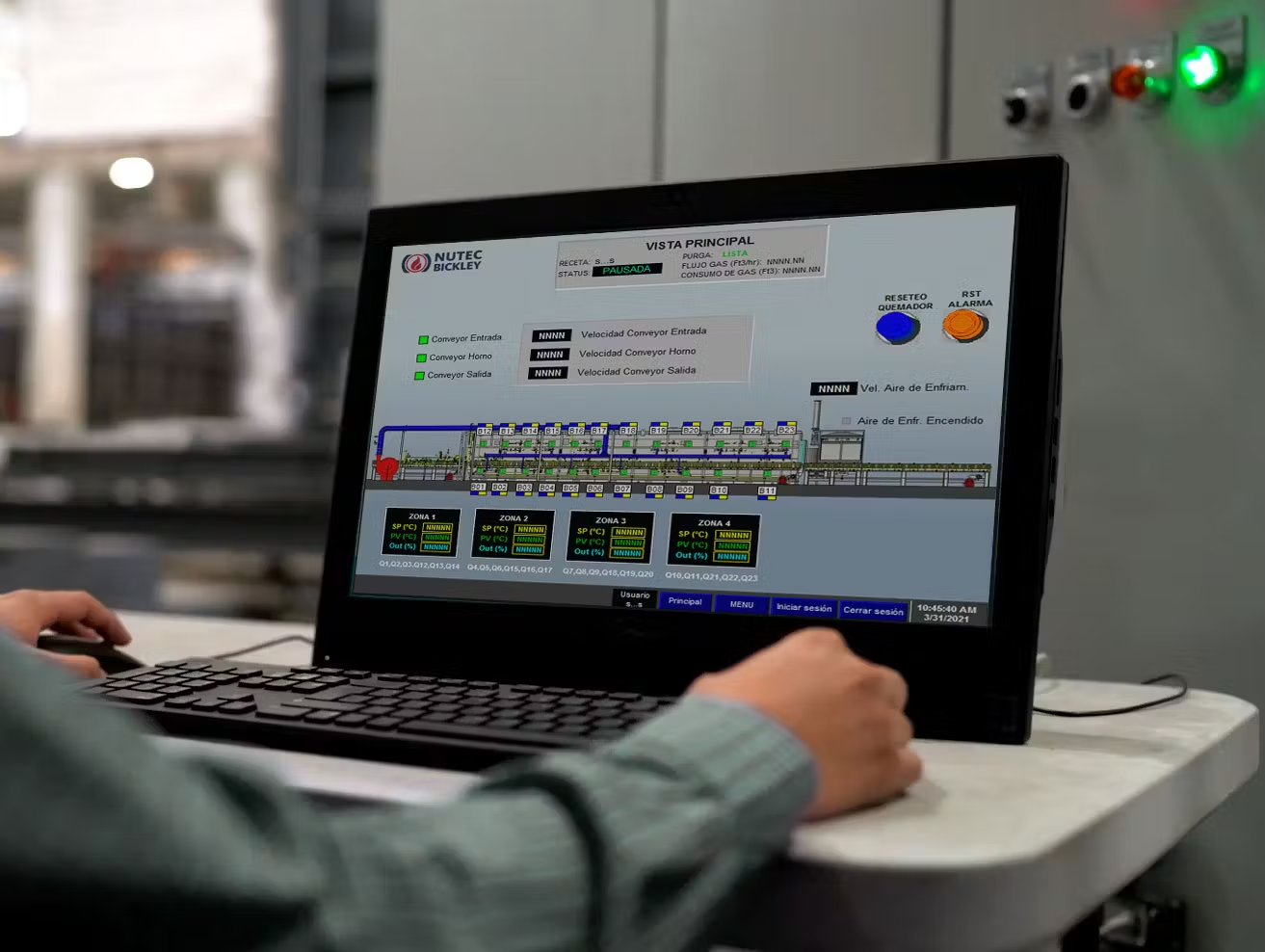
SCADA
With our SCADA systems, kilns operators are able to have complete control of their firing process, enhancing efficiency and productivity.
Learn more about SCADA